about WÜRNHER cOMPANY
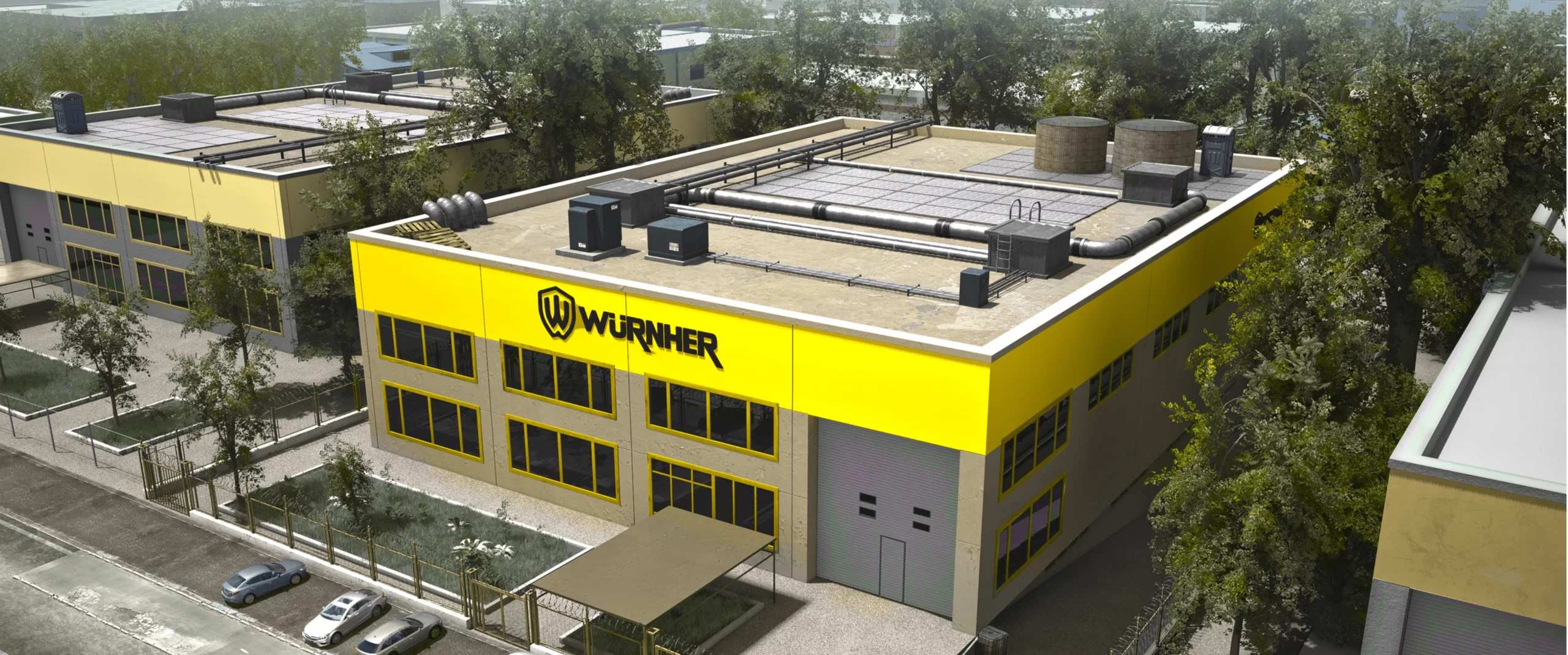
WÜRNHER Co., founded in 2006, with more than 100 employees, is a global high-tech enterprise focused on the production of innovative machining tools and solutions. We have earned a reputation as a pioneering leader in the industrial community thanks to our cutting-edge technologies along with our ability to offer high-quality services.
WÜRNHER Manufacturing plant is located in Bursa. However, it has a global distribution network that enables us to service the world market. We guarantee that our WÜRNHER has service and support available to you, no matter where you are.
WÜRNHER conducts activities in three business areas: research and development (R&D), production, and sales of their products and services. Our top tech experts and experienced professionals in each of these areas are trying to support client demands and promote their success. We have a comprehensive product category that may be utilized in all sorts of machining. These products include indexable cutting tools, solid tools, tool holders, and indexable cemented carbide inserts. Combining different grades of these cutting tools allows for turning, milling, boring, drilling, parting, grooving, and threading processes.
WÜRNHER always adheres to viable product innovation, which is supported by the R&D concept. As a result, the firm has prioritized effective R&D strategies to propel the industry forward and improve machining technology for the benefit of our valued customers. Additionally, our professionals collaborate closely with specialized teams and acknowledged worldwide partners to produce high-quality forward-compatible products and optimized solutions.
WÜRNHER aims to be a prominent domestic and international provider of machining cutting tools trusted by our customers. We believe that high-quality products and services equal customer satisfaction and higher revenue.
Thank you for choosing us.
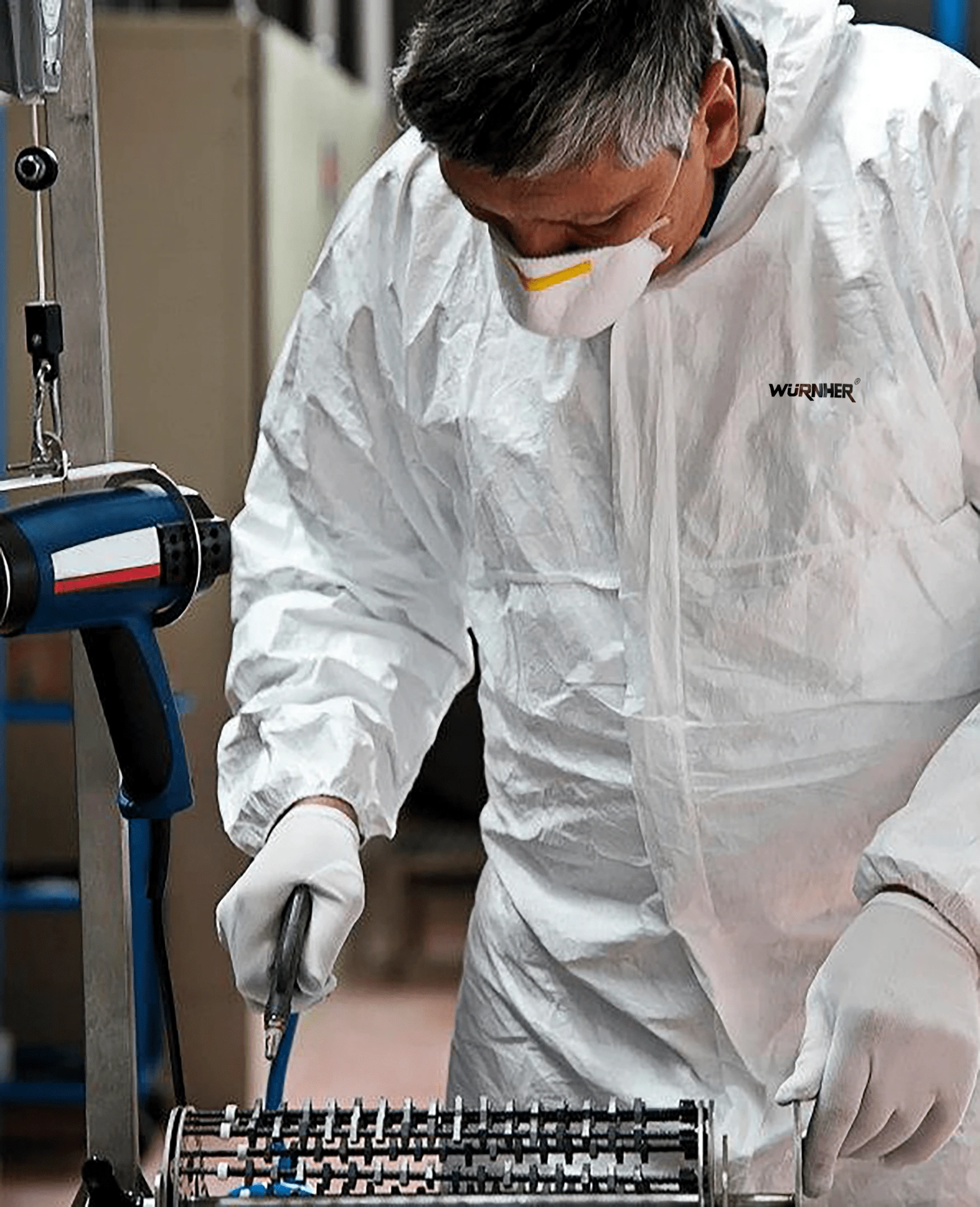
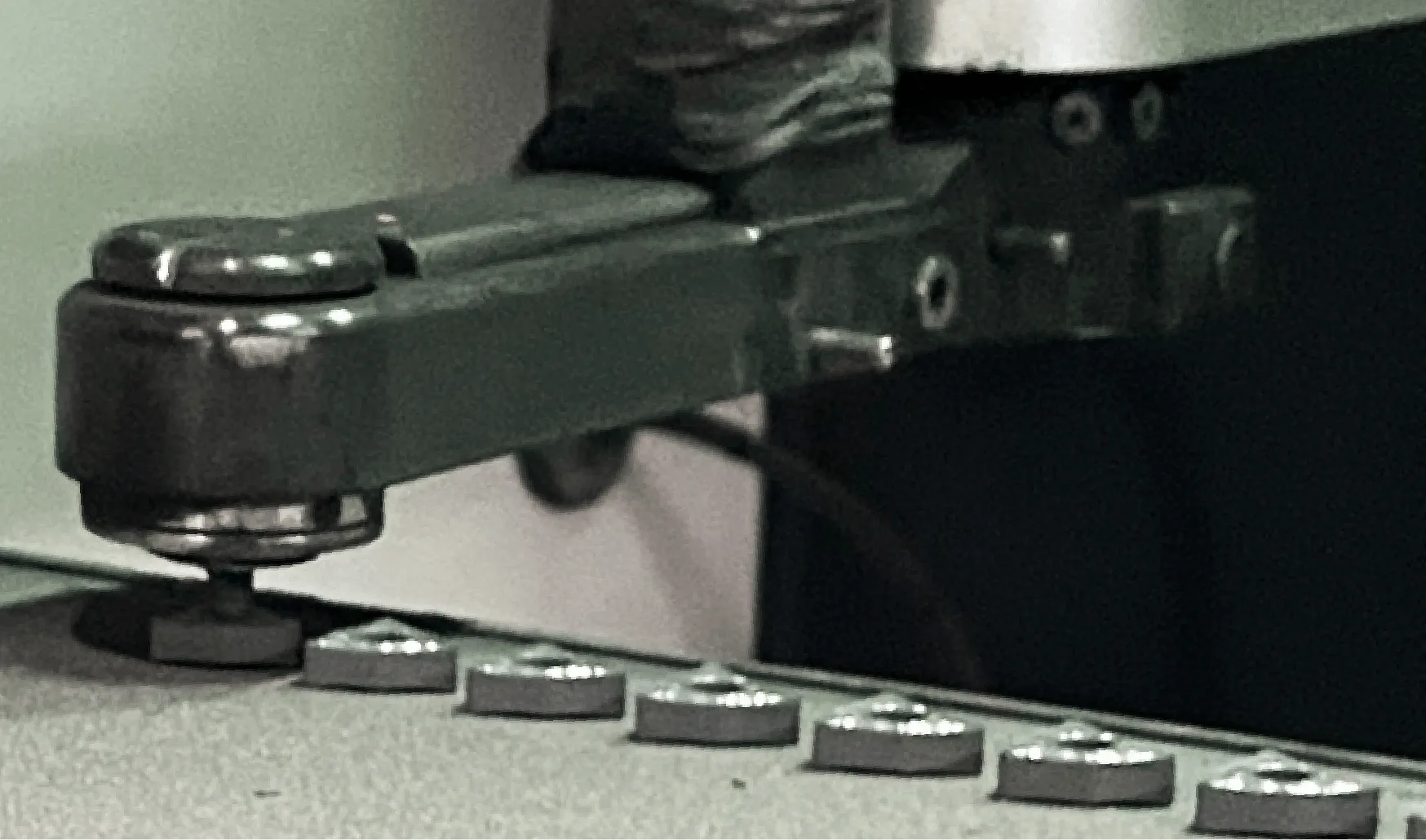
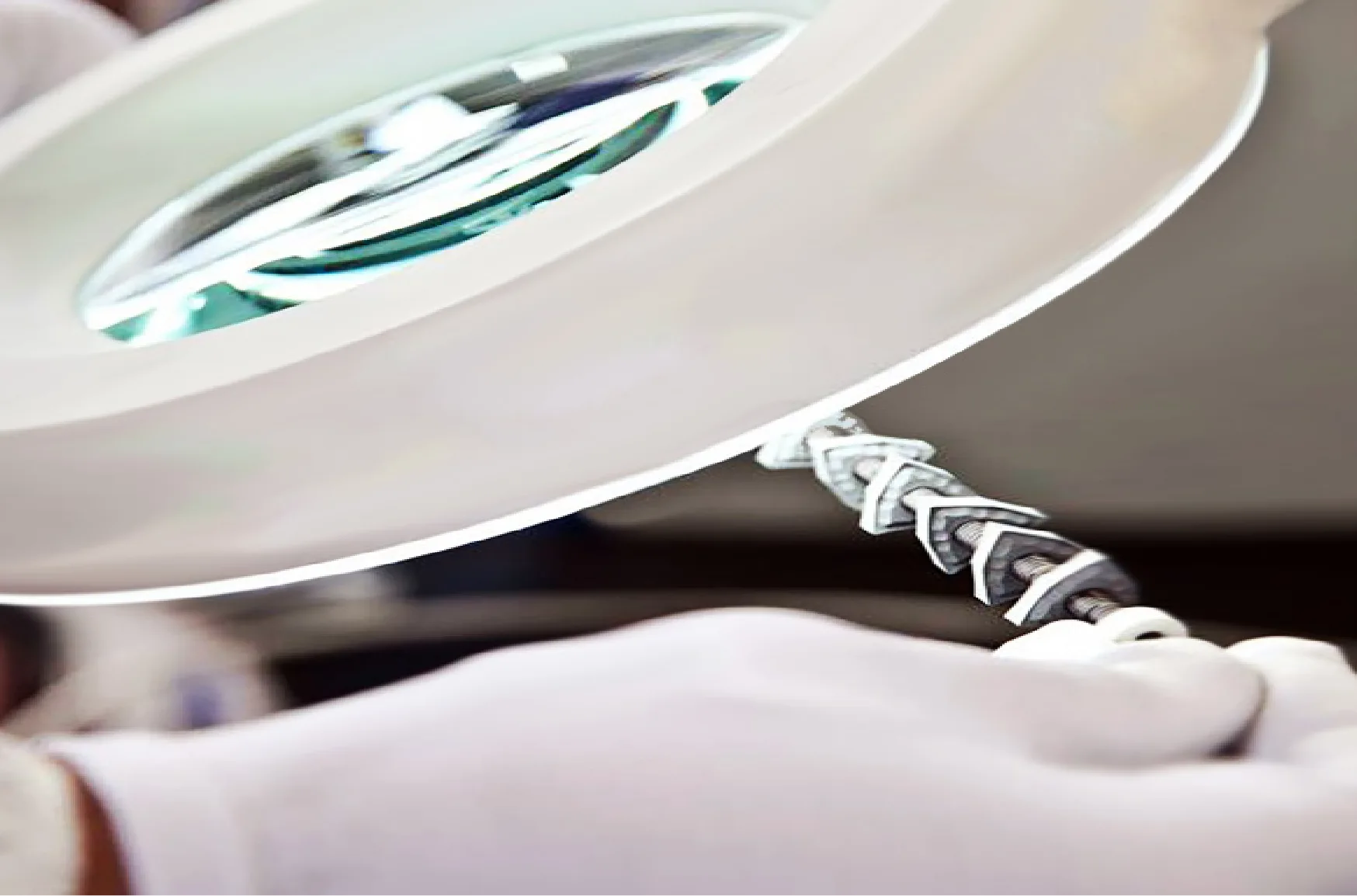
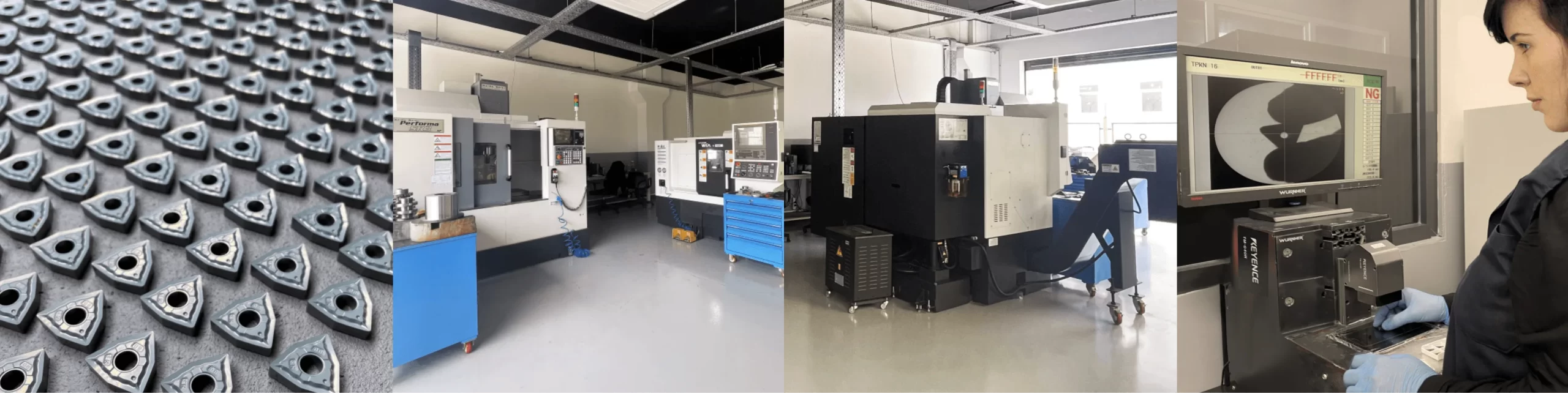
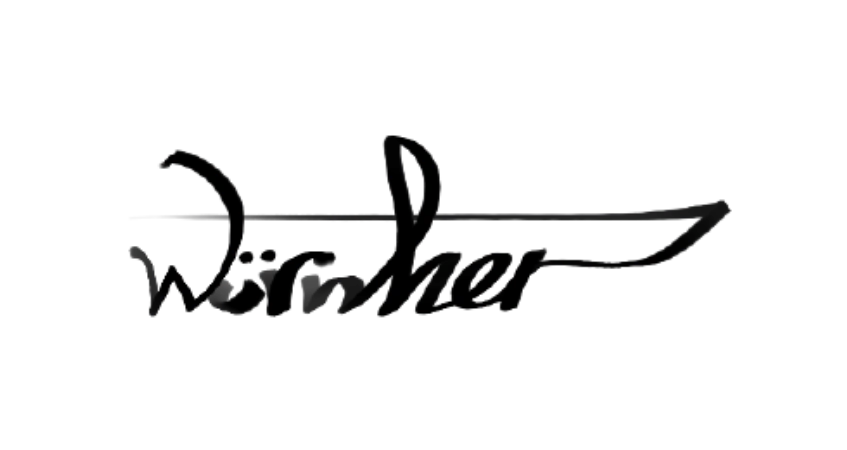
WHAT WE DO
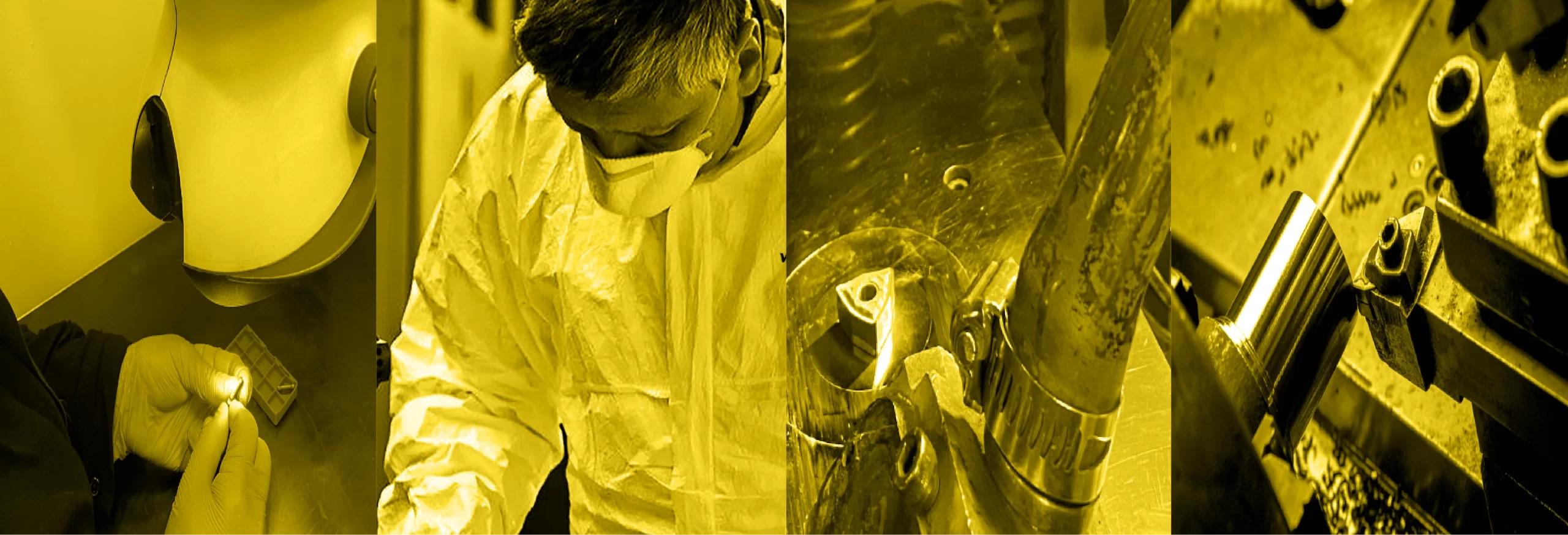
PRESSING
Herein, you will learn about the pressing procedure used in the manufacturing process of carbide inserts. The raw materials for inserts, which are mostly composed of cobalt and tungsten carbide in different combinations, are initially as a powder. This mixture is fed through a fully automated, CNC-controlled press that has dies and punches to enable it to be pressed into the required basic shape and size until it achieves moderate strength. The operator controls this procedure visually. Take note that the insert breaks quickly at this stage and is quite fragile.
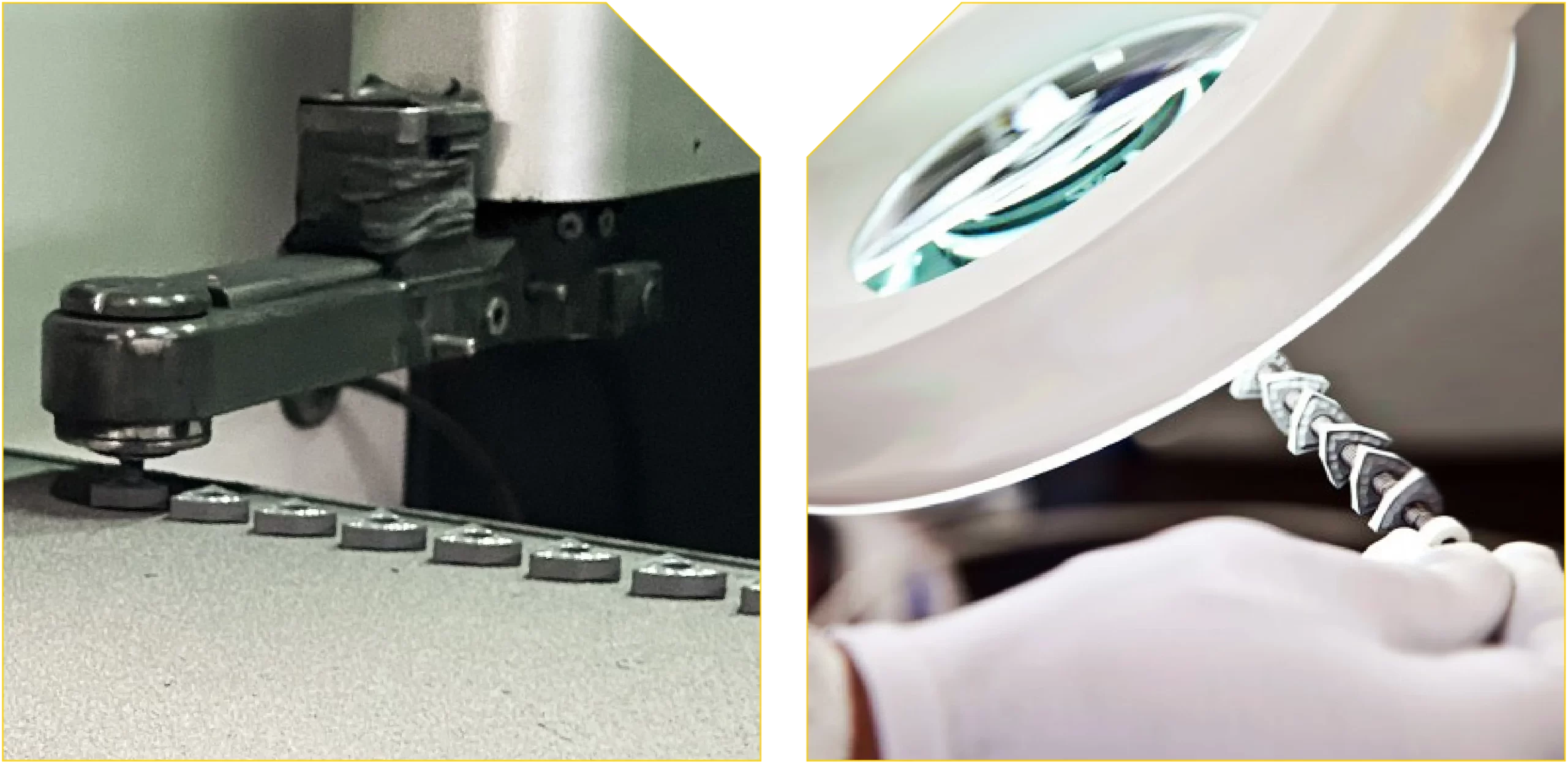
SINTERING
The pressed insert is heat treated in a sintering furnace to approximate 1500 degrees Celsius, which is above the melting point of cobalt and below the melting point of tungsten carbide as the harder phase, in order to create a dense hard insert. Thousands of inserts can be held simultaneously in the furnace. Consider that the insert shrinks during the sintering process, and distortion may also result depending on the density distribution following the pressing procedure. Understanding the relation between pressing process parameters and the final shape is crucial because it affects the tolerances of the final product.
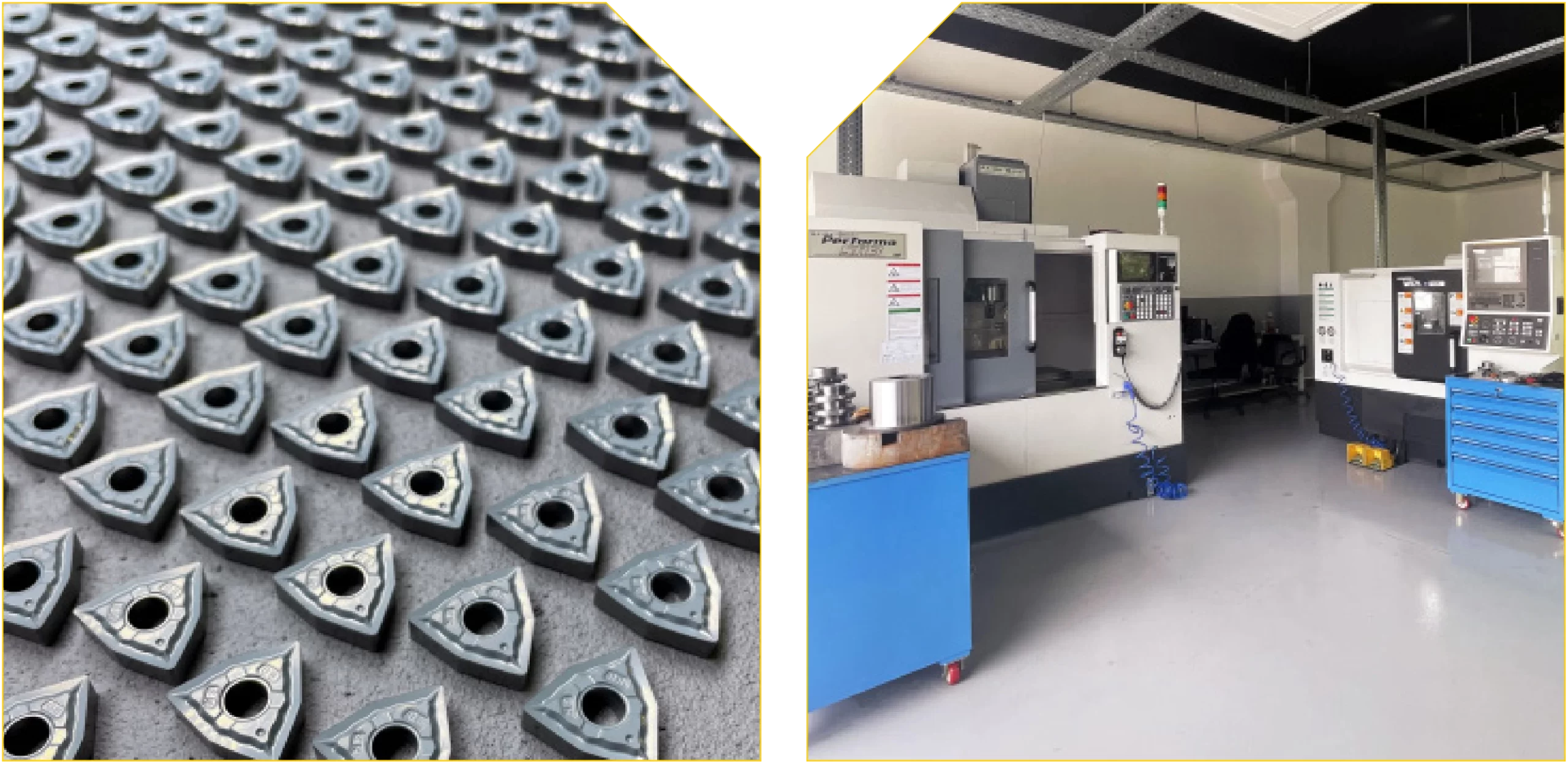
Quality Control
The quality controls in the manufacturing process of carbide inserts make it possible to guarantee that they fulfill their function appropriately. Our QC team thoroughly inspects all products for high quality before delivery. They utilize technical solutions based on modern technologies to ensure that insert dimensions and tolerances conform to the design specifications. They also assess coating thicknesses to ensure they meet requirements and evaluate the thickness variations. Similarly, all inspections are performed with regard to the standards, as appropriate, to verify the product’s high quality.
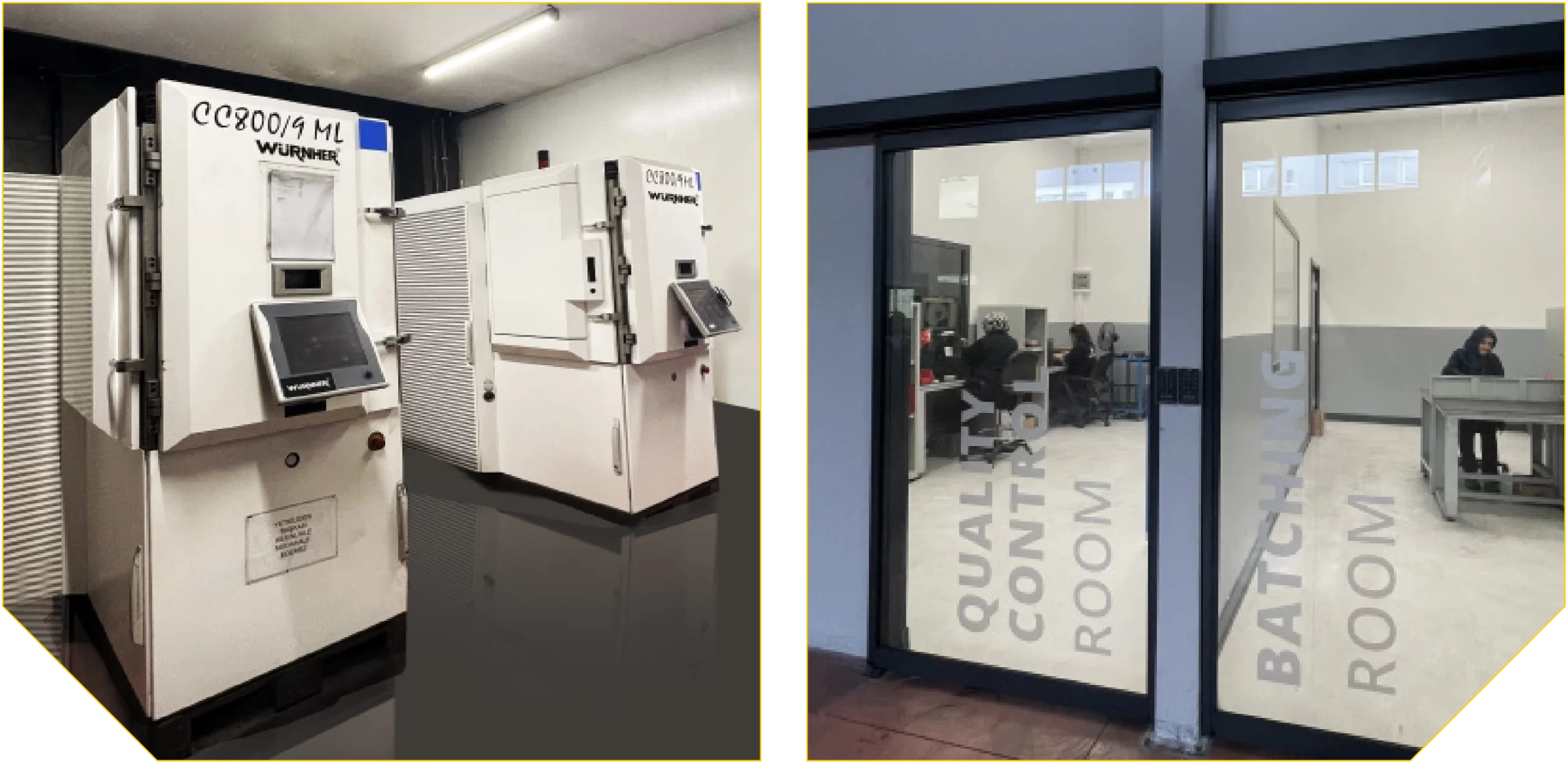
TECH CENTER
Our mission is to provide high-quality products and exceptional customer service. This can only be accomplished by empowering the company’s technical center. Our technical experts’ primary tasks are to gather and analyze qualitative and quantitative technical data to evaluate the performance of the product and determine the optimum machining parameters from the viewpoints of the machine and the workpiece material. This allows them to define standard benchmarking points that enable them to compare products considering the intended purpose of each. Other responsibilities of the technical center staff include looking for the simplest and most cost-effective solution to the customer’s technical challenge. Our technical center ensures that the best ideas drive the product in the production chain.
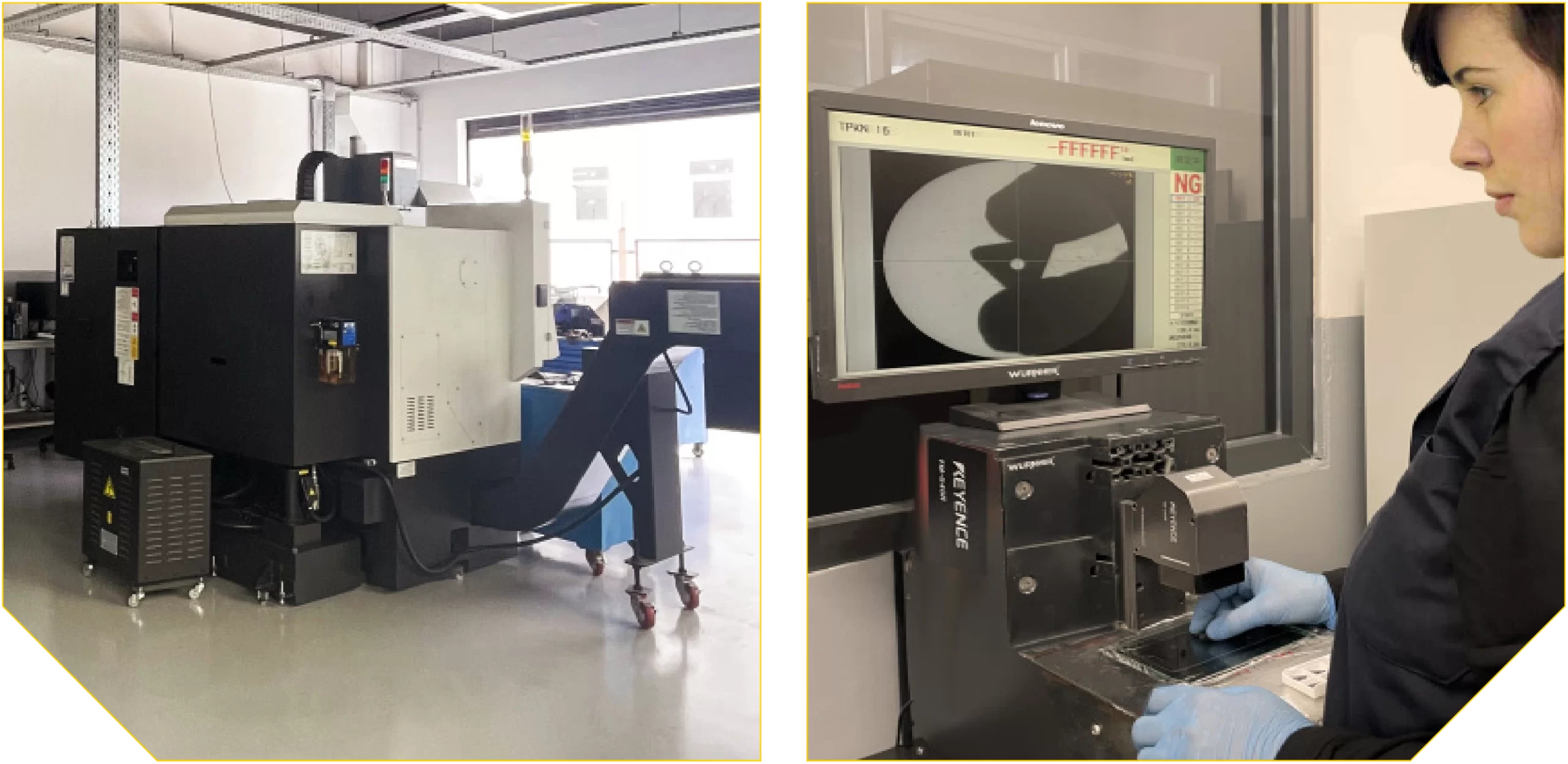